Hot Dip Galvanizing
Technical specification
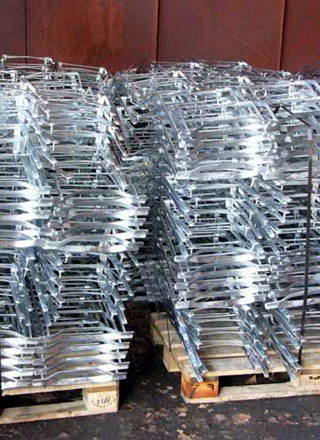
Technology description
Since March 2004, ERLEN has been carrying out hot-dip galvanizing in its own galvanizing plant located in Fulnek on the site of the former ROMO plant.
The galvanizing plant is unique for its “wet zinc” technology, which achieves exceptional quality of galvanized goods. Hot-dip galvanizing provides long-term anti-corrosion protection for steel products. Steel components are dechlorinated in hydrochloric acid to remove rust, scale and impurities. The demoralised material is fed into molten zinc via ammonium chloride, where the zinc is applied to the goods. The uniqueness of the “wet zinc” technology lies in the fact that the ammonium chloride is placed directly over a portion of the molten zinc (the mirror), thus preventing oxidation of the iron in the galvanizing process. Products galvanized in this way have a high gloss and exceptional surface quality.
The graph shows the ideal silicon content in iron, where a content from 0-0.3% and from 0.12-0.2% Si is ideal for the quality of the zinc layer.
Zinc coating options
and 6.5 m x 1.4 m x 3 m)
and 16.2 m x 1.9 m x 2.75 m)
Requirements for input material
The quality of the galvanized material, and thus the satisfaction of our customers, is our primary goal. In order to supply the best quality material, we need to follow certain input material guidelines. These principles are governed by EN ISO 1461 and EN ISO 14713-1 for hot dip galvanizing. In particular, the input material should meet the following criteria:
If you are in any doubt about the properties of the material you are supplying for galvanizing, please contact our professionals who will be happy to provide you with expert assistance.
References
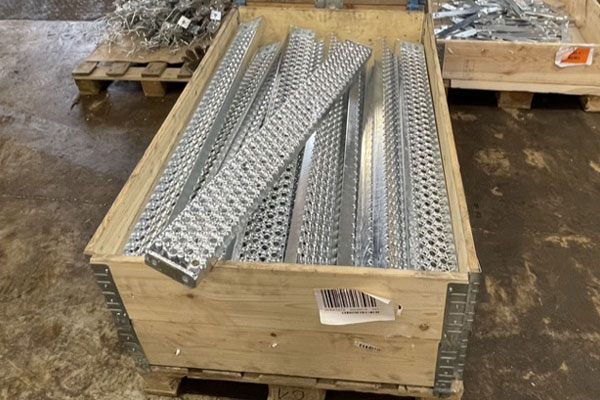
Steps
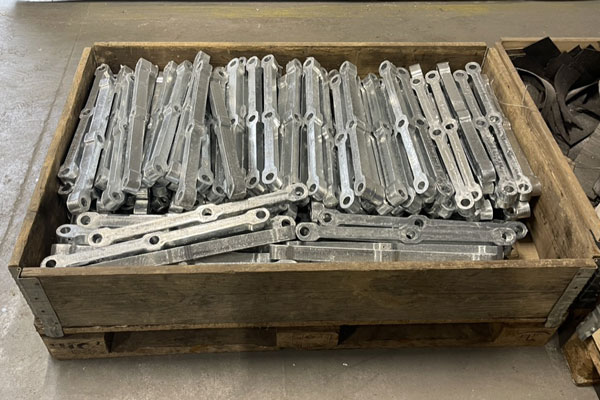
Connecting rods
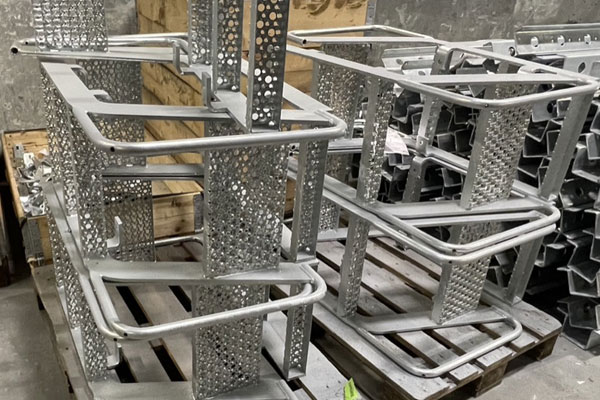
Treads
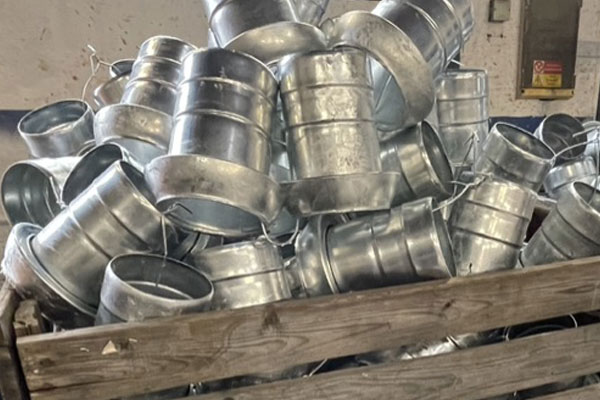
Irrigation systems parts
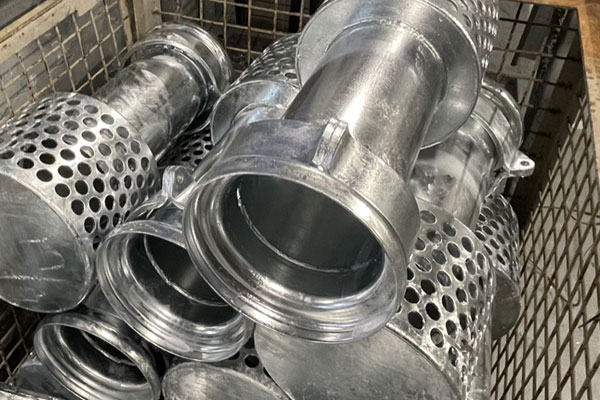
Pump components
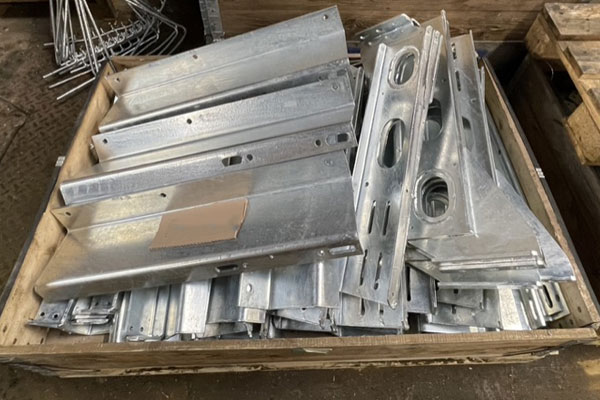